As mentioned above, this research has particular relevance due to lack of information about the use of additives like superplasticizers in hydraulic lime grouts, compared to the amount of information that exists in the case of cement. The natural hydraulic lime was adopted because their chemical and physical properties are closer to those of the pre-existing materials of the masonry, thus minimizing the consequences of the use of cement in rehabilitation interventions, which may end up by causing more damage than benefits because of the possible interaction of cement with the original materials used in the old stone masonry.
Based on the previous idea the research was developed with the objective of determining which type and dosage of dispersing additive provides greater compatibility with the hydraulic lime used in grouts. The dispersant additives used were superplasticizers based on naphthalene and polycarboxylates. The superplasticizers based on naphthalene belong to the second generation of superplasticizers, whose action of dispersion of binder results from electrostatic repulsion resulting from ionization of the binder particles with identical charges.
The superplasticizers based on polycarboxylate belong to the third generation, with a dispersive action resulting from the joint effect of electrostatic repulsion and steric repulsion. The steric repulsion is a consequence of the molecular structure which prevents the approach of the binder particles. In this step it was analyzed which type of superplasticizers presented a better compatibility with hydraulic lime and what is their optimal dosage.
Flow tests on the Marsh cone were conducted to determine the flow time for different contents of each superplasticizer with constant water / binder ratio and mixing procedure. The research team concluded that the superplasticizer based on naphthalene is the one that presents better performance with hydraulic lime because it preserves the fluidity of the grouts for a longer time when compared to the superplasticizer based on polycarboxylate.
Before starting the optimization of grout composition, it was necessary to assess the best sequence of introduction of grout constituents during the mixing process. This task consisted on the determination of the influence of grout mixing process in the rheological properties, based on analysis of the following parameters:
- Delay of the addition of superplasticizers;
- Amount of water used at the beginning and during the addition of superplasticizer;
- Mixing speed;
- Mixing time.
Since it is known that the first requirement for a grout to be injectable is to have low viscosity and high stability, several laboratory tests were performed to achieve an appropriate mixing procedure that optimizes grout properties. So, the influence of different parameters (upper mentioned) on several grout properties (such as apparent viscosity, water retention and stability) were evaluated using the concept of design of experiments together with the Taguchi method.
Based on the achieved results the following points are to be emphasized: (i) a delay on superplasticizer addition of 10 min improves the particles dispersion that leads to an improvement of the grout fluidity; (ii) an initial water amount of 70% induces a more stable mix with better rheological behaviour (lower viscosity); (iii) the mixing speed of 800 rpm produces a better mixture than others higher speeds; (iv) 3 min of mixing time after superplasticizer addition represents enough mixing time to ensure a homogenous superplasticizer diffusion.
These results were compiled and they are reported in the following paper:
Baltazar L.G., Henriques F.M.A., Jorne F. (2012) Optimisation of flow behaviour and stability of superplasticized fresh hydraulic lime grouts through design of experiments. Construction and Building Materials Journal 35: 838-845, Elsevier.
Injection grout performance is affected by a large number of parameters, including additive type and dosage, water/binder content as well as environmental conditions, mixing time, mixer type, energy and sequence of mixing. Hence, and as a first step in this research work, the optimization of mixing procedure was made. Likewise, evaluation of the effect of different additives in the grout behaviour was performed in order to choose which ones should be used in grout composition.
Then, the optimization of grout composition based on the ability of grout to perform as desired was made, which was assessed using fresh properties measured in the laboratory, such as its yield stress and plastic viscosity, among others. Injection grouts based on hydraulic lime binder are colloidal suspensions in which the particle interactions may lead to the formation of various microstructures, which leads to complex interaction and, therefore alter the flow field.
Temperature is a factor that strongly influences how such grout microstructure responds and evolves in time. Thus, the effect of temperature on the grout flow properties was studied in order to better understand the flow behaviour of hydraulic lime grouts under different environmental temperatures.
In addition and complementarily to these different experimental techniques was used to understand the complex physics and chemistry governing grout injection into masonry filler materials, in order to develop optimized strategies for improved grout treatments and a to arrive at a more fundamental understanding of the grout injection process.
First the injection tests were performed using reduced models; these models were filled with a porous medium, which characteristics reproduce the inner core of a masonry wall. The observed invasion behaviours were correlated with preparation and injection parameters, in order to rationalize the optimization of composition and injection procedures as well as some prior preparation of porous medium (like pre-wetting).
The effectiveness of injection (of those reduced models) was studied through the combination of non-destructive techniques (ultrasonic tomography) together with destructive techniques (mechanical strength tests) for a better accuracy determination of injection quality.
As mentioned above, this research has particular relevance due to lack of information about the use of additives like superplasticizers in hydraulic lime grouts, compared to the amount of information that exists in the case of cement. The natural hydraulic lime was adopted because their chemical and physical properties are closer to those of the pre-existing materials of the masonry, thus minimizing the consequences of the use of cement in rehabilitation interventions, which may end up by causing more damage than benefits because of the possible interaction of cement with the original materials used in the old stone masonry.
Based on the previous idea the research was developed with the objective of determining which type and dosage of dispersing additive provides greater compatibility with the hydraulic lime used in grouts. The dispersant additives used were superplasticizers based on naphthalene and polycarboxylates. The superplasticizers based on naphthalene belong to the second generation of superplasticizers, whose action of dispersion of binder results from electrostatic repulsion resulting from ionization of the binder particles with identical charges.
The superplasticizers based on polycarboxylate belong to the third generation, with a dispersive action resulting from the joint effect of electrostatic repulsion and steric repulsion. The steric repulsion is a consequence of the molecular structure which prevents the approach of the binder particles. In this step it was analyzed which type of superplasticizers presented a better compatibility with hydraulic lime and what is their optimal dosage.
Flow tests on the Marsh cone were conducted to determine the flow time for different contents of each superplasticizer with constant water / binder ratio and mixing procedure. The research team concluded that the superplasticizer based on naphthalene is the one that presents better performance with hydraulic lime because it preserves the fluidity of the grouts for a longer time when compared to the superplasticizer based on polycarboxylate.
Before starting the optimization of grout composition, it was necessary to assess the best sequence of introduction of grout constituents during the mixing process. This task consisted on the determination of the influence of grout mixing process in the rheological properties, based on analysis of the following parameters:
- Delay of the addition of superplasticizers;
- Amount of water used at the beginning and during the addition of superplasticizer;
- Mixing speed;
- Mixing time.
Since it is known that the first requirement for a grout to be injectable is to have low viscosity and high stability, several laboratory tests were performed to achieve an appropriate mixing procedure that optimizes grout properties. So, the influence of different parameters (upper mentioned) on several grout properties (such as apparent viscosity, water retention and stability) were evaluated using the concept of design of experiments together with the Taguchi method.
Based on the achieved results the following points are to be emphasized: (i) a delay on superplasticizer addition of 10 min improves the particles dispersion that leads to an improvement of the grout fluidity; (ii) an initial water amount of 70% induces a more stable mix with better rheological behaviour (lower viscosity); (iii) the mixing speed of 800 rpm produces a better mixture than others higher speeds; (iv) 3 min of mixing time after superplasticizer addition represents enough mixing time to ensure a homogenous superplasticizer diffusion.
These results were compiled and they are reported in the following paper:
Baltazar L.G., Henriques F.M.A., Jorne F. (2012) Optimisation of flow behaviour and stability of superplasticized fresh hydraulic lime grouts through design of experiments. Construction and Building Materials Journal 35: 838-845, Elsevier.
The influence of some inorganic additives such as silica fume and fly ash, and organic additives, such as superplasticizer and air entraining agent in the fresh and hardened grout performance was made. Then, the optimization of grout composition based on the rheological data was made. From a durability point of view, the analysis of microstructure evolution of the grout with additives and its mechanical characterization was made. Finally, the influence of environmental temperature on rheological properties and thixotropy of grouts was studied.
According with the results obtained, the following conclusions can be drawn on the influence of different additives on some relevant properties of injection grouts, from the masonry consolidation point of view:
i) The hydraulic lime replacement by fly ash results in a slight decrease in yield stress. Nevertheless, the presence of fly ash leads to a decrease in grout compressive strength.
ii) The results indicate that superplasticiser is the additive that most contributes to a better grout performance, from the rheological, stability and water retention point of view.
iii) The presence of silica fume together with superplasticiser allows a significant improvement in the grout stability.
iv) The grouts with fly ash and superplasticiser show the best rheological behaviour i.e. the lowest yield stress and plastic viscosity.
v) Air entraining agent is by far the worst additive, since it leads to the worst grout performance, even when compared with the plain hydraulic lime grout.
It was clear that, from a comprehensive point of view considering fresh and hardened-state results, products like superplasticiser are essential when designing a grout for injection purposes and its presence seems to be particularly required when other powder additives are used, such as silica fume.
Following the previous results, the effects of grout composition on their fresh behaviour was studied with the purpose of a successful injection process. Using a rotational rheometer together with the Taguchi method it was possible to study the influence of water/binder ratio, the dosage of superplasticizer and the partial replacement of hydraulic lime by silica fume, upon the grout rheological properties. Based on the rheological requirements for a successful grout injection of masonry, an attempt to achieve an optimal grout composition was made. Several results were obtained showing that water/binder ratio and superplasticizer dosage are the most determinant factors in the fresh grout behaviour.
An increase in dosage of these two factors resulted in a more fluid grout. The use of silica fume revealed a poor contribution on the rheological behaviour of hydraulic lime grouts since increased amounts of silica fume lead to worse performance. Since silica fume is much finer than hydraulic line particles, superplasticizer available per surface area decreases, resulting in a more viscous grout.
However, silica fume replacement up to 10wt% can be considered acceptable from the perspective of rheological performance; moreover, it was found that the presence of silica fume increases the grout stability, i.e. with lower final bleeding, besides the improvement of grout properties in the hardened state. Since, from porosity measurements (by mercury intrusion) show a reduction of open porosity which represents a good result since the grout strength will be improved.
Taking into account the advantages of silica fume in the fresh and hardened grout behaviour the research team chose to study this variable alone as a replacement of hydraulic lime. Thus, the effects of silica fume in improving the hydraulic lime grout compressive strength and other hardened properties were studied. It was used the hydraulic lime replacement by silica fume in different levels (0 - 25wt%).
The research team concluded that the silica fume decreases the grout porosity and permeability, and increases its strength. The reduction of total pore volume in grout with silica fume is caused by the high pozzolanic reactivity (between the SiO2 in the silica fume and Ca(OH)2 from hydration products) and the pore-filling effect caused by the very small particles of silica fume. The small silica fume particles might have packed efficiently between the hydraulic lime grains, and thereby subdivided the pore space, thus creating a much denser pore structure. Therefore, there may be referred that silica fume acts both physically (as filler) and chemically (reacting with Ca(OH)2 to form C-S-H) to aid in the strength improvement.
This way the benefit of adding silica fume is twofold: decreasing total pores volume and increasing compressive strength. In fact the analysis of the results indicate that, in all mixes at 28 days after curing, increasing the silica fume content in the hydraulic lime paste also increased the compressive strength. The results obtained also shown a reasonable linear correlation between the capillary coefficient and the silica fume content, allowing predicting the capillary absorption of the water in hydraulic lime grouts with silica fume in their composition. Results of the capillary sorptivity show that pastes with higher silica fume content uptake less water amount, and this can be a way to prevent deterioration of material. Based on the conclusions achieved it is suggested that both the strength and durability of hydraulic lime grouts could be improved by the usage of silica fume.
The effect of temperature on the grout rheological properties was studied through rheometric measurements in order to better understand the flow behaviour of NHL-based grouts under different environmental temperatures. Thus, the effect of different environmental temperatures in range of 5 to 40ºC on the yield stress and plastic viscosity was studied. According with the results obtained, the following conclusions can be highlighted:
The evolution of yield stress and plastic viscosity values with increase of temperature suggests that at low temperatures, 5ºC, the formation of ice crystals may occur leading to higher yield stress and plastic viscosity. However, with the increase of temperature both rheological parameters decrease as results of the thermal agitation; nevertheless, for temperatures above 20ºC this thermal agitation is countered by two factors, such as faster reaction kinetics of the lime hydration and the increase in electrostatic forces of lime particles with temperatures.
Thereby, it can be stated that the environmental temperature of 20ºC is the one that leads to the best grout rheological performance.
As far as grout thixotropy is concerned, two different factors are likely involved in the thixotropic behaviour: (i) Temperature increase that leads to faster hydration reactions and higher flocculation state. Moreover, the growth of hydration products on the surface of the binder particles will cover the adsorbed layers of superplasticizer which results in a progressive loss of superplasticizer dispersion action. (ii) At lower temperatures (such as 5 ºC) the grout temperature begins to approach to the water freezing point, which leads to formation of strong hydrogen bonds. In turn, at the molecular level, temperature is related to the random motions of the particles (Brownian motion) as previously mentioned.
This means that for lower temperatures, the molecular agitation decreases (grout particles are closer to each other), thus a less freedom state causes a higher flocculation (quicker microstructure build up). In addition, it is also possible that, at lower temperatures, a decrease in the intensity of the dispersion mechanism of superplasticizer molecules may occur, caused by changes in the spatial arrangement of the adsorbed superplasticizer. Note, however, that high flocculation rate can be the solution to solve some problems after injection; for instance when grout is at rest inside the masonry, gravity may induce sedimentation of grout particles at rest. So, a high flocculation rate can be useful since it will increase the shear stress which can be sufficient to prevent the particles from settling.
These results were compiled and are reported in the following papers:
- Baltazar L.G., Henriques F.M.A., Jorne F., Cidade M.T. (2013) The use of rheology in the study of the composition effects on the fresh behaviour of hydraulic lime grouts for injection of masonry walls. Rheologica Acta 52(2): 127-138, Springer
- Baltazar L.G., Henriques F.M.A., Cidade M.T. (2014) Contribution to the design of hydraulic lime-based grouts for masonry consolidation. Journal of Civil Engineering and Management (accepted for publication on January 2013), Taylor & Francis
- Baltazar L.G., Henriques F.M.A., Jorne F., Cidade M.T. (2014) Combined effect of superplasticizer, silica fume and temperature in the performance of natural hydraulic lime grouts. Construction & Building Materials 50: 584-597, Elsevier.
In order to determine the best injection pressure a preliminary campaign (before injection testes) using a pressure cell – Bohlin HPC300 – attached to the rotational rheometer (see fig) was performed. The effect of pressure on grout rheological properties was studied, and the injection pressure that is less harmful on grout rheological performance was determined. The influence of several pressures in range of 0.5 to 1.5bar on different rheolgical parameters was studied. Additionally a grout without pressure (i.e. analysed at atmospheric pressure) was used as reference sample.
As long as grout injection pressure is concerned, several authors have stated that grout injection can be done with a pressure over a range of 0.2–1.0 bar. Accordingly, the injection pressure is crucial in grouting process because, on one hand, the injection pressure should be high enough so that high shear rates prevail inside the injection pipe and, consequently, a decrease in viscosity occurs, and on the other hand, it must not be too high (limited to a few bars) in order to avoid any structural damage caused by the internal pressure within the masonry the influence of pressure on the rheological properties.
As expected, there was an increase of the yield stress as well as of the plastic viscosity with the increase of pressure. However, it was clear that the difference between the grout at pressure of 0.5 bar and the one without pressure was actually negligible. The major difference in terms of rheological parameters occurs for pressures higher than 1 bar. So, taking into account the results obtained, and the fact that the injection pressure should be limited to a sufficient low pressure to avoid the masonry disruption, but as high as possible in terms of the injection itself (rheological performance), an injection pressure of 1bar was adopted to be used on the injection tests in physical models.
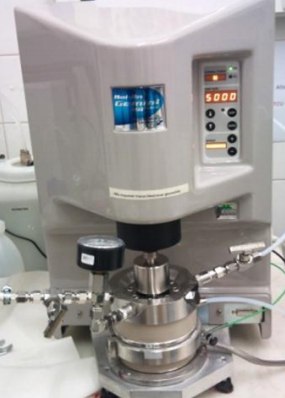
The efficacy of the grouts depends mainly on the injectability properties, rather than the simple hardened characteristics of the mixtures. Therefore, it is essential to evaluate the effectiveness of the injections in terms of keeping the properties of the mixtures that are considered as adequate. So, the efficiency of grout injection in porous media simulating old masonries, by analysing the performance of the grout injection capacity as a function of the porous medium to be injected was made in this step.
The injections tests were performed on reduced models filled with the different porous media; the aims were to understand the grout flow inside the porous media and to establish a relation between the grout injection capacity and the different parameters associated to porous media, namely permeability, voids volume, water content, grain size distribution, contact angle and water absorption capacity of particles.
The main goals of injection tests were the following:
- evaluate the minimum fineness of the porous media that allows the chosen grout to be injected;
- understand the grout flow inside porous media for the different grain size distributions used;
- observe the relationships between injection capacity of grout and media grain size distributions.